- TheCobotReport
- Posts
- #01 TheCobotReport
#01 TheCobotReport
Summer is over, cobots are here...

While you've been sipping your morning coffee, the cobot world’s been quietly cranking up the safety dial with the latest ISO 10218-1/2 updates redefining the standards. But that’s just the tip of the robotic arm.
Buckle up, because this week’s newsletter dives into everything you need to stay ahead in the world of cobots!
In this week’s email…
Quick Hit: ISO 10218-1/2 Updates: Raising the Bar for Cobot Safety.
Movers & Shakers:
ABICOR BINZEL's iBOTone: Welding's New Best Friend ABICOR BINZEL.
ABB’s GoFa Cobots Upgrade: Game-Changer in Precision Additive Manufacturing.
Graduate Corner: Exploring a visualization tool that enhances cobot debugging for more efficient pick-and-place applications.
Upcoming Events: Key conferences and workshops to keep on your radar in the robotics and AI fields.

In the news…
PickGPT, LLMs meet robotics. How large language models are revolutionizing robotic capabilities with natural language commands.
Universal Robots showcases enhanced the payload capacity of its UR20 and UR30 cobots, allowing them to lift 25 kg and 35 kg respectively through a software update.
Chipolte’s Autocado cobot might be preparing your next burrito bowl.
Flexiv's Rizon 4 robot automates fish fillet shaping with AI-powered precision.
Premier Tech unveils game-changing TomaCobot for packaging and palletizing.

QUICK HIT:
ISO 10218-1/2 Updates: Raising the Bar for Cobot Safety
The cobot landscape is shifting as safety standards catch up with technological advancements. The recent updates to the ISO 10218-1 and ISO 10218-2 standards aim to address the challenges of integrating cobots into industrial environments.
These revisions focus on enhancing risk assessments, safety function verification, human-robot collaboration, and cybersecurity measures to ensure safer and more efficient operations. This means the industry is moving from coexistence (Industry 4.0) to a collaborative model (Industry 5.0), where human-robot interactions are expected to be smoother and safer.
The inclusion of the collaborative robotics specifications from ISO/TS 15066 means manufacturers must consider cobots' interactions with humans more carefully.
Additionally, integrating cybersecurity measures is essential, given that over 3.5 million industrial robots are in use today - a figure that has doubled since 2016. By applying these safety protocols, companies can mitigate potential hazards and improve operational efficiency.
The need for these standards is underscored by real-world incidents.
These incidents demonstrate that as we move into Industry 5.0, the importance of safety compliance, like adopting a micro kernel-based real-time operating system, cannot be overstated. It’s essential for creating fault-tolerant, reliable, and secure environments where humans and robots can truly collaborate.

MOVERS & SHAKERS:
1 . ABICOR BINZEL's iBOTone: Welding's New Best Friend ABICOR BINZEL
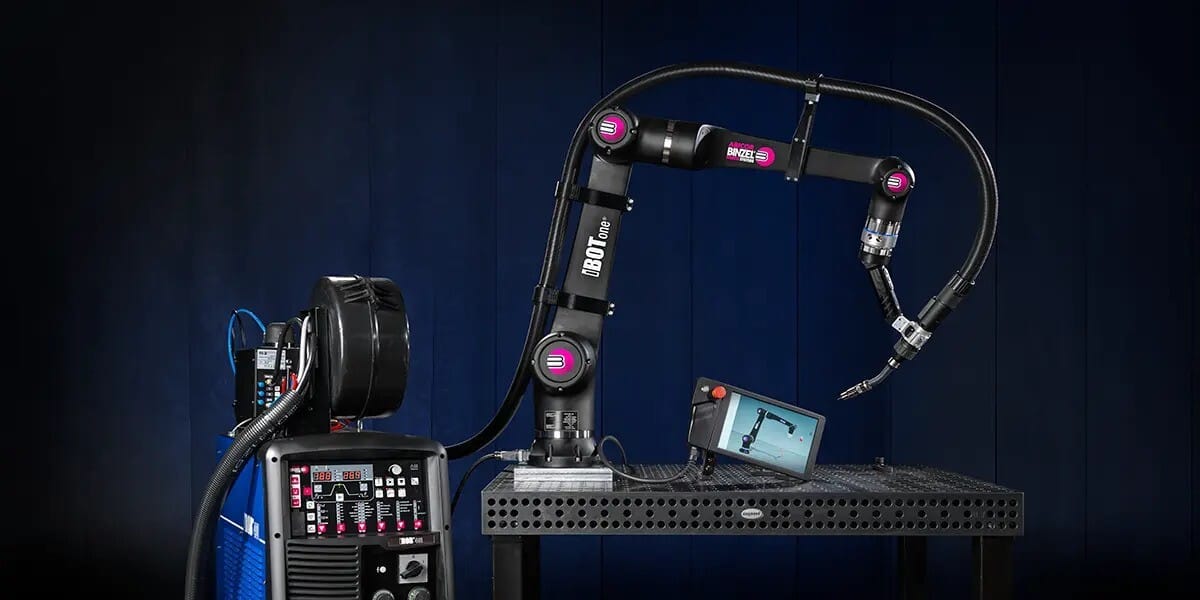
Image courtesy of ABICOR BINZEL
ABICOR BINZEL has introduced the iBOTone, a welding cobot that brings precision and user-friendly design to industrial welding. This collaborative robot is designed to work alongside human operators, enhancing both productivity and quality.
The iBOTone offers consistent, high-quality welds, ensuring that every joint is precisely executed. Its intuitive control system makes it easy to program, even for those who are new to welding. Safety is a priority, with built-in features allowing it to operate safely around human workers, while its compact, 6-axis design enables seamless integration into existing production lines.
In terms of technical specifications, the iBOTone offers a reach of 1,400 mm, a payload capacity of 6 kg, and operates at speeds up to 2 meters per second with a power supply of 220 V AC. This cobot is more than just a welding tool; it represents an upgrade to the entire manufacturing workflow.
Faster welding processes lead to increased output, fewer defects, and reduced costs. The iBOTone is suitable for industries such as automotive, aerospace, metal fabrication, and agriculture, proving to be a versatile addition to modern manufacturing.
Investors, take note: The iBOTone isn't just about welding; it's about upgrading your entire workflow. Faster welding means more output, fewer defects, and reduced costs. It's perfect for industries like automotive, aerospace, metal fabrication, and even agriculture.
2. ABB GoFa Cobots Upgrade: Game-Changer in Precision Additive Manufacturing
ABB's latest Ultra Accuracy GoFa CRB 15000 cobots are revolutionizing additive manufacturing by addressing some of the industry's most pressing challenges.
Traditional 3D printing often faces limitations in achieving the precision needed for high-tolerance applications, such as aerospace and medical devices, where even minor dimensional inaccuracies can be problematic. This can result in surface quality issues, wasted materials, and slower production cycles, especially for complex parts requiring consistent detailing.
The GoFa cobots, with their remarkable 0.03 mm path accuracy, offer a tenfold increase in precision over previous models. This leap forward ensures the production of high-quality, consistent parts, significantly reducing the need for manual intervention and recalibration.
By featuring payload capacities from 5 kg to 12 kg and a reach of up to 1.6 meters, they are highly adaptable for medium to large-scale manufacturing tasks. Additionally, the cobots' advanced motion control and force detection technologies enable real-time adjustments, ensuring accuracy even with intricate designs.
In essence, ABB's cobots are not just a technological upgrade - they represent a transformative step in overcoming the limitations of traditional additive manufacturing, enhancing both precision and productivity. For more details, you can check out ABB’s official page here and the comprehensive article on 3DPrint.com.
Investors, take note: ABB’s Ultra Accuracy GoFa cobots are poised to transform the additive manufacturing market. Their unmatched precision, safety features, and adaptability make them ideal for industries like aerospace, automotive, and construction, where accuracy and efficiency are crucial.
With the ability to streamline production, reduce waste, and accelerate prototyping, these cobots offer significant potential for cost savings and improved ROI. As the demand for high-quality, customizable 3D-printed products grows, ABB’s technology represents a prime opportunity for investment in the rapidly expanding field of advanced manufacturing.
*Note: Massive Dimension focuses on developing adaptive, customizable robotic cells for the Additive Manufacturing industry, continually expanding applications across various sectors.

GRADUATE CORNER:
Contextual visualizations for debugging collaborative robots
Emil Stubbe Kolvig-Raun, Thor Malmby Jørgin, Miguel Campusano
2024 IEEE/ACM 6th Intl. Workshop on Robotics Software Engineering (RoSE)
The visualization tool integrates runtime data with robot program execution, allowing operators to quickly identify issues and validate the cobot's behavior.
The tool offers insights into the success, failure, and partial success of cobot actions, such as picking up objects, by using data from vacuum grippers and execution steps
This paper presents a novel visualization tool designed to improve the debugging process for collaborative robots (cobots), with a focus on pick-and-place applications.
As cobots are increasingly used in manufacturing environments, the complexity of programming and maintaining them has also grown. Traditional debugging tools often fall short in providing clear insights into the behavior of these robots. To address this, the authors developed a tool that uses dynamic visualizations based on runtime data, helping operators identify and resolve issues in cobot operations.
The tool integrates with the robot's program, allowing users to trace the execution steps in real-time, visualize joint movements, and monitor variables such as vacuum levels in gripping tasks.
The visualization tool not only enables operators to validate the accuracy of a cobot's movements but also helps identify specific sections of the program where failures or inaccuracies occur. This approach significantly enhances the debugging process by providing a more intuitive understanding of cobot behavior, which is crucial for maintaining efficiency and safety in industrial settings.
Upcoming Events:
ANTS (Swarm robotics) 2024 : Oct-09-2024 | Konstanz, Germany
IROS 2024 : Oct-14-2024 | Abu Dhabi, Emirate of Abu Dhabi
RoboBusiness : Oct-16-2024 | Santa Clara, United States of America
Reply