- TheCobotReport
- Posts
- #07 TheCobotReport
#07 TheCobotReport
Record Funding, AI Software as Solutions, Additive Manufacturing...

Welcome to this week’s edition where, we’re covering record-breaking investments, groundbreaking innovations in AI-driven robotics, and transformative advancements in metal additive manufacturing.
In this week’s email…
Quick Hit: Strategic Insights: Articulated Industrial Robots Market Poised to Reach $92 Billion by 2032.
Movers & Shakers:
Revolutionizing Metal Additive Manufacturing with Meltio Engine Robot Integration
Transforming Additive Manufacturing with AiBuild's AI-Powered Software
Graduate Corner: Automated Weld Path Generation in Cluttered Environments using Segmentation and Iterative Closest Point Work-piece Localization.
Upcoming Events: Key conferences and workshops to keep on your radar in the robotics and AI fields.

In the news…
Robotics Investments Surpass $3.7 Billion in September 2024: The robotics sector experienced a significant surge in September 2024, with companies securing over $3.7 billion in funding, marking the highest monthly total for the year.
Physical Intelligence Secures $400 Million to Develop Generalist AI for Robotics: Startup Physical Intelligence has raised $400 million to advance foundation models aimed at enabling robots to perform a wide range of tasks with minimal programming.
Vision-Guided Robot Enhances Uniformity in Breaded Fish Fillets: Flexiv has introduced a vision-guided robotic system capable of shaping breaded fish into consistent fillets, improving efficiency in seafood processing.
Omron Unveils TM25S Collaborative Robot with Enhanced Reach and Payload: Omron has launched the TM25S, a collaborative robot featuring a 25 kg payload capacity and a 1900 mm reach, designed for applications such as palletizing and welding.
Doosan Robotics Introduces High-Payload Cobots at Pack Expo 2024: Doosan Robotics showcased its latest high-payload collaborative robots, including the P3020 model with a 66 lbs payload and 6-foot reach, tailored for palletizing tasks.

QUICK HIT:
Strategic Insights: Articulated Industrial Robots Market Poised to Reach $92 Billion by 2032
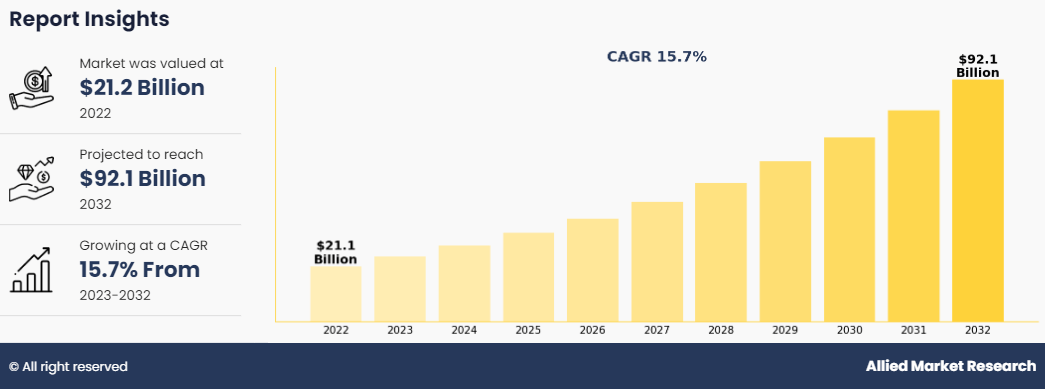
Image courtesy of Allied Market Research
The articulated industrial robot market is a rapidly growing sector, projected to soar from $21.15 billion in 2022 to $92.08 billion by 2032, achieving an impressive CAGR of 15.7% over the forecast period. This growth reflects rising global demand for automation across industries such as manufacturing, automotive, electronics, and logistics. Investors should consider the key drivers, market leaders, and opportunities shaping this lucrative space.
Key Market Drivers:
Cost-Effective Automation Solutions:
Small and medium-sized enterprises (SMEs) are adopting affordable robots to boost productivity without significant capital investment.
Technological advancements like 3D printing, enhanced sensors, and improved actuators are reducing production costs.
Human-Robot Collaboration (HRC):
A growing preference for collaborative robots (cobots) that ensure workplace safety and efficiency.
Increased adoption in dynamic and human-centered work environments.
Industry-Specific Demand:
Adoption in automotive, electronics, and logistics is being driven by the need for precision in tasks such as material handling, welding, assembly, and painting.
Segment Highlights:
Robot Type: Six-Axis Robots dominate the market, accounting for over 40% of global revenue in 2022. Their human-arm-like versatility makes them indispensable for a variety of tasks, including assembly line duties and welding automation.
Load Capacity: Robots in the 10kg to 100kg range hold the largest market share, contributing to over 40% of total revenue in 2022. These robots' ability to handle diverse applications positions them for continued leadership.
Application: Assembly tasks generate the largest revenue, contributing 33% to global market share in 2022. The demand stems from the need for speed and accuracy in production lines.
Growth Drivers by Numbers:
Enhanced Safety: Technological improvements in sensors and AI-enabled robots are reducing risks in human-robot collaboration.
Efficiency Boost: By replacing labor-intensive tasks, articulated robots significantly lower operational costs.
Precision Demand: Robots are increasingly used in high-precision applications such as micro-assembly and advanced material handling.
Technological Enablers:
AI and Machine Learning: Robots with AI capabilities are learning and adapting to dynamic environments, offering tailored solutions in real-time.
Advanced Sensors: Improvements in sensor technology enhance motion accuracy, critical for precision applications.
Control Systems: Simplified programming enables faster deployment and flexibility across tasks.
Closing Thoughts:
With the articulated robot market set to quadruple in value by 2032, now is the time for investors to tap into this high-growth industry. Companies delivering cost-effective, collaborative, and technologically advanced solutions are positioned to lead the future of automation.

MOVERS & SHAKERS:
1 . Revolutionizing Metal Additive Manufacturing with Meltio Engine Robot Integration

Image courtesy of Solidprint3d
In the evolving landscape of cobots, the Meltio Engine Robot Integration stands out as a transformative solution for industries aiming to enhance their metal additive manufacturing capabilities. This innovative system enables the conversion of standard robotic arms into sophisticated metal 3D printing units, effectively removing traditional size constraints and broadening the scope of manufacturing possibilities.
Who Benefits from the Meltio Engine Robot Integration?
The Meltio Engine Robot Integration is designed for a diverse range of industries, including aerospace, automotive, energy, and manufacturing sectors, that require the production of large, complex metal components. It is particularly advantageous for organizations seeking to:
Expand Manufacturing Capabilities: By integrating with existing robotic systems, companies can enhance their production processes without the need for extensive new infrastructure.
Optimize Part Repair and Maintenance: The system facilitates efficient repair of metal parts, extending their lifespan and reducing downtime.
Innovate in Design and Production: With the ability to create intricate geometries, manufacturers can explore new design possibilities that were previously unattainable or cost-prohibitive.
Key Benefits of the Meltio Engine Robot Integration
Scalability and Flexibility: The system integrates seamlessly with any robot arm manufacturer and interface, allowing for customization based on specific operational needs.
Enhanced Geometric Freedom: It enables the creation of highly complex parts with infinite degrees of freedom, overcoming traditional manufacturing limitations.
Cost-Effective Part Repair: The integration provides new capabilities to any robot arm by turning it into a metal 3D printing system, facilitating cost-effective component repair, part augmentation, and feature addition.
Large-Scale Production: With no inherent constraints, the working envelope is only limited by the size of the motion system, making it ideal for large-scale metal 3D printing.
Material Versatility: The system supports a variety of wire materials, including stainless steels, mild steels, carbon steels, titanium alloys, and nickel alloys, catering to diverse manufacturing requirements.
Advanced Process Control: Features such as closed-loop laser and wire modulation, along with optional upgrades like dual wire and hot wire systems, enhance precision and efficiency in the manufacturing process.
Investors take note: Meltio's strategic partnerships with 12 leading software companies to foster hybrid and robotic additive manufacturing adoption underscore its commitment to innovation and market expansion. The company's focus on growth, including new expanded facilities and plans for more wire-laser metal 3D printing innovation, further highlights its potential for sustained development.
2. Transforming Additive Manufacturing with AiBuild's AI-Powered Software

Image courtesy of Automation Fair
In the rapidly evolving field of additive manufacturing, AiBuild offers an advanced software solution that integrates artificial intelligence to enhance 3D printing processes. This platform is designed to streamline production, improve efficiency, and ensure high-quality outputs across various industries.
Target Audience for AiBuild's Software
AiBuild's software caters to a wide range of sectors, including aerospace, automotive, construction, energy, marine, and art and design. It is particularly beneficial for organizations aiming to:
Optimize Manufacturing Workflows: By leveraging AI-driven insights, companies can refine their production processes, reducing time and costs.
Enhance Product Quality: The software ensures precision and consistency, leading to superior product quality.
Scale Production Efficiently: AiBuild's platform supports scalability, allowing businesses to expand their manufacturing capabilities seamlessly.
Construction Industry: AiBuild's software enables the production of large-scale, complex concrete structures through automated 3D printing, enhancing design flexibility and reducing construction time.
Aerospace Manufacturing: The platform facilitates the creation of lightweight, high-strength components, such as turbine blades, by optimizing toolpaths for additive manufacturing, leading to improved fuel efficiency and performance.
Automotive Production: AiBuild's solution allows for rapid prototyping and production of customized parts, including interior panels and brackets, streamlining the design process and accelerating time-to-market.
Marine Engineering: The software supports the fabrication of large, corrosion-resistant components like propeller blades, ensuring precision and durability in harsh marine environments.
By adopting AiBuild's AI-powered software, industries can achieve significant advancements in their manufacturing processes, leading to increased efficiency, reduced waste, and enhanced product quality.
Investors take note: AiBuild's innovative approach to integrating AI with additive manufacturing positions it as a leader in the industry. The company's ability to deliver scalable, efficient, and high-quality manufacturing solutions across multiple sectors highlights its growth potential. Investors should consider AiBuild's strategic vision and technological advancements as indicators of its promising trajectory in the evolving manufacturing landscape.

GRADUATE CORNER:
Automated Weld Path Generation in Cluttered Environments using Segmentation and Iterative Closest Point Work Piece Localization
Tristan Hill, Hyung-Jin Yoon, and Stephen Canfield
Tennessee Technological University
Journal of Mechanisms and Robotics October 22, 2024
Objective: Develop a method for automated weld path generation in cluttered environments by accurately identifying and localizing workpieces using segmentation and Iterative Closest Point (ICP) algorithms.
Approach: Utilize RGB-D cameras to capture 3D data, apply segmentation techniques to isolate the workpiece from clutter, and employ ICP for precise workpiece localization, facilitating automated welding path planning.
The paper "Automated Weld Path Generation in Cluttered Environments using Segmentation and Iterative Closest Point Workpiece Localization" addresses the challenges faced by small to medium enterprises (SMEs) in adopting robotic welding automation due to the complexities of traditional systems.
The authors propose a method that leverages RGB-D cameras to capture 3D data of the workspace, even in cluttered environments. By applying segmentation techniques, the system isolates the workpiece from surrounding clutter. Subsequently, the Iterative Closest Point (ICP) algorithm is employed to accurately localize the workpiece within the workspace. This precise localization enables the automated generation of weld paths, reducing the need for manual setup and increasing the flexibility and efficiency of robotic welding operations in dynamic manufacturing settings.
Investors take note: This approach to automated weld path generation presents a scalable opportunity to disrupt the SME manufacturing segment by reducing barriers to robotic welding adoption. By combining segmentation and ICP-based localization, the solution promises cost-efficiency, adaptability in dynamic environments, and minimal manual intervention—features highly valued by SMEs aiming to increase production agility. This innovation aligns with the growing trend of Industry 4.0, making it a potentially lucrative investment in the advanced manufacturing technology space.
Upcoming
AI World Congress: Nov-27-2024 | London, UK
Reply